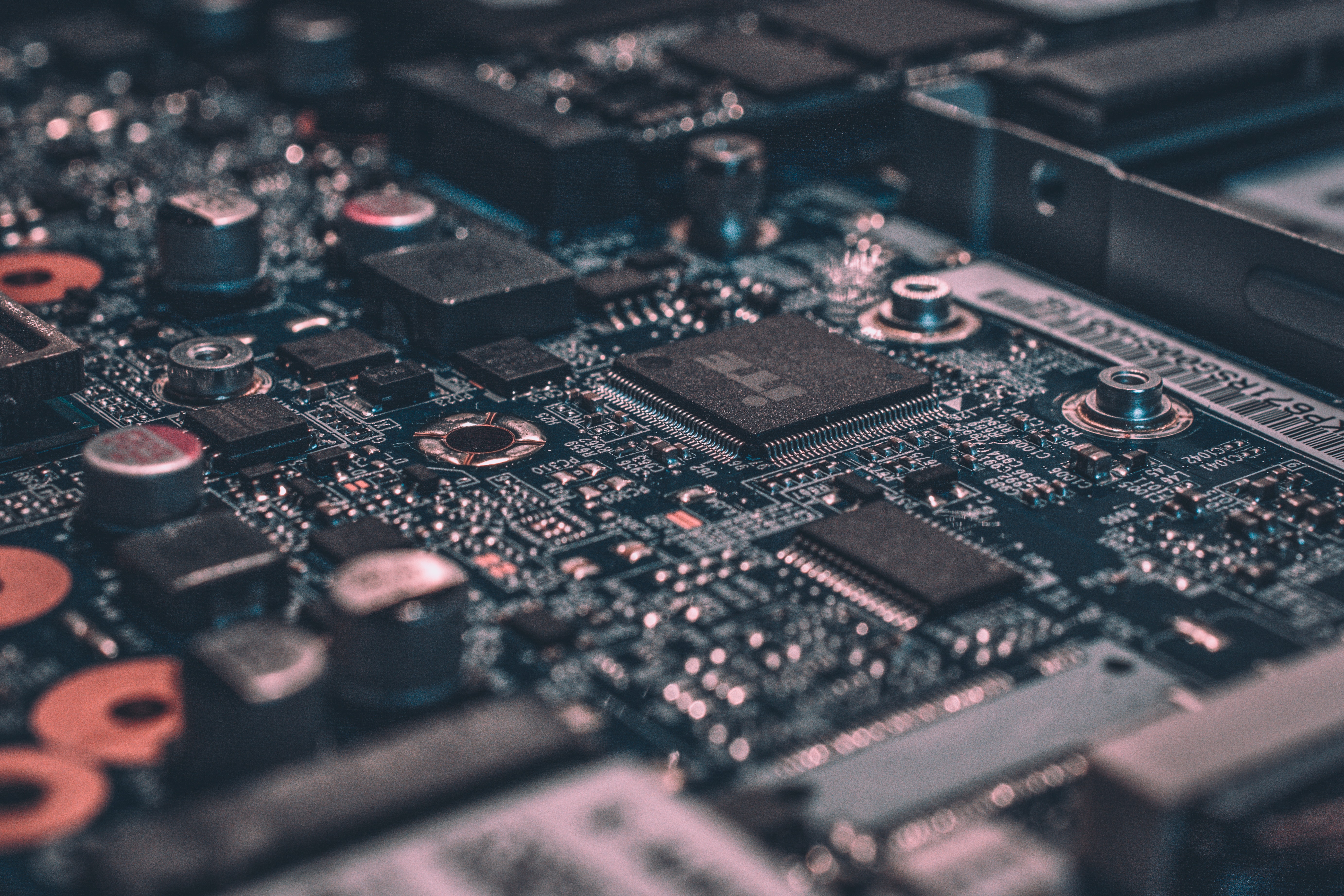
There are many different types of printing, but two of the most common are offset and flexo printing. So, what is the difference between these two printing methods?
Offset printing is a type of printing that uses a plates to transfer an image onto a substrate. Flexo printing is a type of printing that uses a flexible plate to transfer an image onto a substrate.
The main difference between offset and flexo printing is the type of plate that is used. Offset printing uses a rigid plate, while flexo printing uses a flexible plate. This means that flexo printing is typically used for printing on substrates that are not flat, such as corrugated cardboard.
Another difference between offset and flexo printing is the inking process. In offset printing, the inks are rolled onto the plate and then transferred to the substrate. In flexo printing, the inks are applied directly to the substrate.
Flexo printing typically uses water-based inks, while offset printing typically uses oil-based inks. This is because water-based inks are easier to clean up and they dry more quickly. Oil-based inks are more durable and produce a higher quality image, but they are more difficult to clean up and they take longer to dry.
Offset printing is more expensive than flexo printing. This is because offset printing requires the use of more sophisticated equipment and the process is more labor-intensive.
Flexo printing is best suited for short runs of prints, while offset printing is best suited for large runs of prints. This is because flexo printing is a faster process and it is easier to set up.
So, what is the difference between offset and flexo printing? Offset printing uses a rigid plate to transfer an image onto a substrate, while flexo printing uses a flexible plate to transfer an image onto a substrate. Flexo printing is typically used for printing on substrates that are not flat, such as corrugated cardboard.
What are the benefits of flexo printing?
Flexography, also known as flexo printing, is a printing technology using a flexible printing plate. It is one of the most versatile printing processes available, and can be used for printing on a wide variety of substrates, including paper, board, film, and foil.
Flexo printing has several advantages over other printing processes. One advantage is that it can print on a variety of substrates. This flexibility makes flexo printing well suited for print applications that require printing on both paper and non-paper substrates, such as labels and packaging.
Another advantage of flexo printing is that it can print on both sides of a substrate simultaneously. This feature is called simultaneous duplex printing, and it is not possible with most other printing processes. Simultaneous duplex printing can significantly increase production speeds and reduce print costs.
Flexo printing also has some unique design capabilities. One such capability is called relief printing. Relief printing is a printing technique in which the image to be printed is raised above the non-printing areas of the printing plate. This raised image can then be inked and transferred to the substrate. Relief printing is not possible with most other printing processes, making flexo printing ideal for applications requiring this printing technique.
Overall, flexo printing is a versatile, efficient, and cost-effective printing technology. It is well suited for a wide variety of printing applications, including those that require simultaneous duplex printing or relief printing.
Take a look at this: Whatsapp Image
What are the disadvantages of offset printing?
Offset printing is a technique where inked images on metal plates are transferred (or "offset") to rubber mats, then to the printing surface. AlthoughOffset printing has many advantages, there are several disadvantages that should be considered when deciding if this printing process is right for your project.
The biggest disadvantage of offset printing is the initial setup cost. This type of printing requires a lot of expensive equipment, including metal plates and rubber mats. In addition, the inks and solvents used in offset printing can be expensive.
Another disadvantage of offset printing is that it can be a slow process. Each color must be printed one at a time, which can take a while if your design is complex. In addition, the drying time between colors can also add to the overall printing time.
Finally, offset printing can sometimes produce poor quality results. This is because the images are transferred from the metal plates to the rubber mats, and then to the printing surface. If any of these steps are done incorrectly, it can result in fuzzy or blurred images.
For your interest: Curved Surface
What are the disadvantages of flexo printing?
Flexo printing has several disadvantages when compared to other printing processes. One significant disadvantage is that it is not as precise as some other methods, such as rotogravure or offset printing. This can be a problem if tight registration is required, or if fine details are part of the design. Additionally, flexo printing generally has a lower image quality than other methods, due to the nature of the medium. The raised areas of the printing plate can cause ink to spread, resulting in blurred or smeared images. Finally, flexo printing is a fairly slow process, so it may not be the best choice for high-volume printing projects.
What are the applications of offset printing?
Offset printing is a printing process where the inked image is transferred (or "offset") from a plate to a rubber blanket and then to the printing surface. While the term "offset printing" can refer to the fact that the image is transferred from the plate to a rubber blanket, it most often refers to the lithographic process of printing.
The offset printing process uses a number of different inking and dyes to create the image, and these inks and dyes are transferred to the rubber blanket. The blanket then transfers the image to the printing surface. The main advantage of offset printing is that it allows for very large print runs with little wear and tear on the printing plates.
Offset printing is used for a wide variety of printing projects, including books, magazines, newspapers, business cards, stationery, and more.
A fresh viewpoint: Silicone Rubber
What are the applications of flexo printing?
Flexo printing is a printing process that uses a flexible printing plate. The process can be used for printing on many different substrates, including paper, cardboard, plastic, and metal. Flexo printing is commonly used for packaging, labels, and other printed materials.
The process of flexo printing begins with the preparation of the printing plate. The design is typically created using a computer-aided design (CAD) program. Once the design is complete, it is transferred to the printing plate. The printing plate is mounted on a cylinder, which is mounted on the printing press.
Ink is then applied to the printing plate. The printing plate cylinder rotates, and the ink is transferred to the substrate. The substrate is then fed through the printing press, and the print is complete.
Flexo printing has several advantages over other printing processes. It is a fast and efficient way to print large quantities of material. The process is also capable of producing high-quality prints.
There are a variety of different applications for flexo printing. The most common applications are package printing and label printing. Flexo printing is also commonly used for point-of-purchase displays, tags, and stickers.
For more insights, see: Screen Sizes for Responsive Design
What are the printing techniques of offset printing?
Offset printing is a printing technique in which ink is transferred from a metal plate to a rubber blanket, and then to the printing surface. It is the most commonly used printing technique in the world and is used for printing books, magazines, newspapers, packaging, and other commercial products. Offset printing has a number of advantages over other printing techniques, including its high efficiency, accuracy, and consistency.
The first step in offset printing is to create a printing plate, which is typically made of aluminum. The printing plate is coated with a light-sensitive material, which is exposed to light through a negative image. The exposed areas of the printing plate are then developed, which creates a raised image on the plate.
The next step is to transfer the image from the printing plate to a rubber blanket. This is done by running the printing plate and the rubber blanket through a set of rollers. The rollers apply ink to the raised areas of the printing plate, which is then transferred to the rubber blanket.
The rubber blanket then transfers the ink to the printing surface. This is done by running the rubber blanket and the printing surface through a set of rollers. The rollers apply pressure to the rubber blanket, which forces the ink onto the printing surface.
Offset printing is a high-speed printing process that can print large quantities of prints quickly and accurately. This makes it ideal for printing newspapers, magazines, books, and other commercial products.
Readers also liked: Commercial Printing
What are the printing techniques of flexo printing?
Flexo printing, also known as Relief printing or Flexography, is a printing process that uses a flexible relief plate to transfer an image onto a substrate. The printing process itself is relatively simple: a design is engraved into a flexible relief plate, inking rollers transfer ink to the plate, and the plate then prints the image onto the substrate.
Flexo printing is one of the most versatile and widely-used printing techniques in the world, capable of printing on a variety of substrates including paper, cardboard, film, and foil. It is commonly used for printing packaging, labels, and newspapers.
Flexo printing has a number of advantages over other printing techniques. It is a relatively low-cost printing method, and it is also fast and efficient. In addition, flexo printing plates can be reused many times, which further reduces the cost of printing.
Flexo printing does have some disadvantages, however. One major disadvantage is that it is not capable of printing very fine details or very small text. In addition, the printing quality can vary depending on the substrate and the skill of the printer.
Overall, flexo printing is a versatile, efficient, and cost-effective printing method that is widely used in a variety of applications.
Readers also liked: Letterpress Printing Cost
Which printing method is better for large print runs?
In the world of printing, there are a few different methods that can be used to print large quantities of material. The two most popular methods are offset printing and digital printing. So, which printing method is better for large print runs?
Let's take a look at offset printing first. Offset printing is a traditional printing method that uses a printing plate to transfer an image onto a piece of paper. This printing method is typically used for large print runs because it is able to print large quantities of material quickly and efficiently. The only downside to offset printing is that it can be quite expensive, especially if you are printing large quantities of material.
Digital printing is a newer printing method that uses a digital file to print an image directly onto a piece of paper. This printing method is becoming increasingly popular for large print runs because it is much cheaper than offset printing. The only downside to digital printing is that it is not as fast as offset printing and it does not produce as high of a quality image.
So, which printing method is better for large print runs? If you are looking for the most efficient and cost-effective method, then digital printing is the way to go. However, if you are looking for the highest quality print, then offset printing is the better option.
A different take: Printing Method
Frequently Asked Questions
Why choose Flexo over offset printing?
There are many reasons why you might want to choose Flexo over offset printing. Here are a few: 1. Higher print speeds: With flexo, you can expect print speeds that are up to 50% faster than traditional offset printing. This means you can get your prints done more quickly and with less wasted time. 2. Greater availability of inks: With flexo, there are a much wider range of inks available that can be used for printing. This means you can get the most precise prints possible, whatever your needs may be. 3. Enhanced color quality: Flexo also typically produces better color quality than offset printing - meaning that your prints will look more vibrant and accurate.
What is the difference between offset printing and regular printing?
Offset printing is a technique that produces a high-quality image by depositing ink onto a substrate, such as paper, and then pressing the print onto an already printed sheet of paper. Regular printing simply prints text or graphics on plain paper.
What is the difference between rotary printing and flexographic printing?
The main difference between rotary printing and flexographic printing is the type of plates used. Rotary printers use flexible plates that are designed for a rotary printing process, while flexographic printers use plates made from a photopolymer compound that can be printed onto with a typical ink-jet printer.
What types of inks can be used in a flexo printing machine?
UV inks, water based ink and solvent ink are among the most popular types of inks used in flexo printing machines.
What is the difference between Flexo and offset printer?
Offset printing is a printing technique that uses an elongated printing plate that is laid down on top of the paper, with the image sent to a series of presses which can then create raised impressions of the image on the paper. Offset printers are more often used for large format printing and usually produce a much higher quality final product than flexo printers. Flexo printers work by bending the paper and heating it up, creating a very smooth finished product.
Sources
- https://packmojo.com/help/offset-printing-flexographic-printing/
- https://www.oren-intl.com/blog/bid/301939/Differences-Between-Flexographic-Gravure-Offset-and-Inkjet-Printing
- https://www.srmindustry.com/Flexo-Printing-vs-Offset-Printing-Three-Top-Differences/
- https://www.slideshare.net/systemelectronics/what-is-the-difference-between-flexo-printing-offset-printing
- https://bizfluent.com/13660198/the-advantages-of-flexo-printing
- http://blog.focuslabel.com/difference-between-offset-and-flexo-printing
- https://www.flexoglobal.com/blog/2014/02/10/advantages-of-flexographic-printing/
- https://ritegraphics.com/advantages-of-flexographic-printing/
- https://blog.mps-printing.com/offset-printing-vs-flexo-printing
- https://texaslabelprinters.com/resources/blog/the-differences-between-flexographic-and-offset-printing/
- https://packmojo.com/blog/offset-printing-vs-digital-printing-vs-flexography-vs-digital-printing/
- https://jeytop.com/advantages-of-flexo-printing-machine/
- https://blog.luminite.com/blog/flexo-printing-vs-offset-printing
- https://www.expresspkg.com/news/advantages-flexographic-printing/
- https://blog.mps-printing.com/a-close-look-at-offset-vs.-flexo-in-label-printing
Featured Images: pexels.com