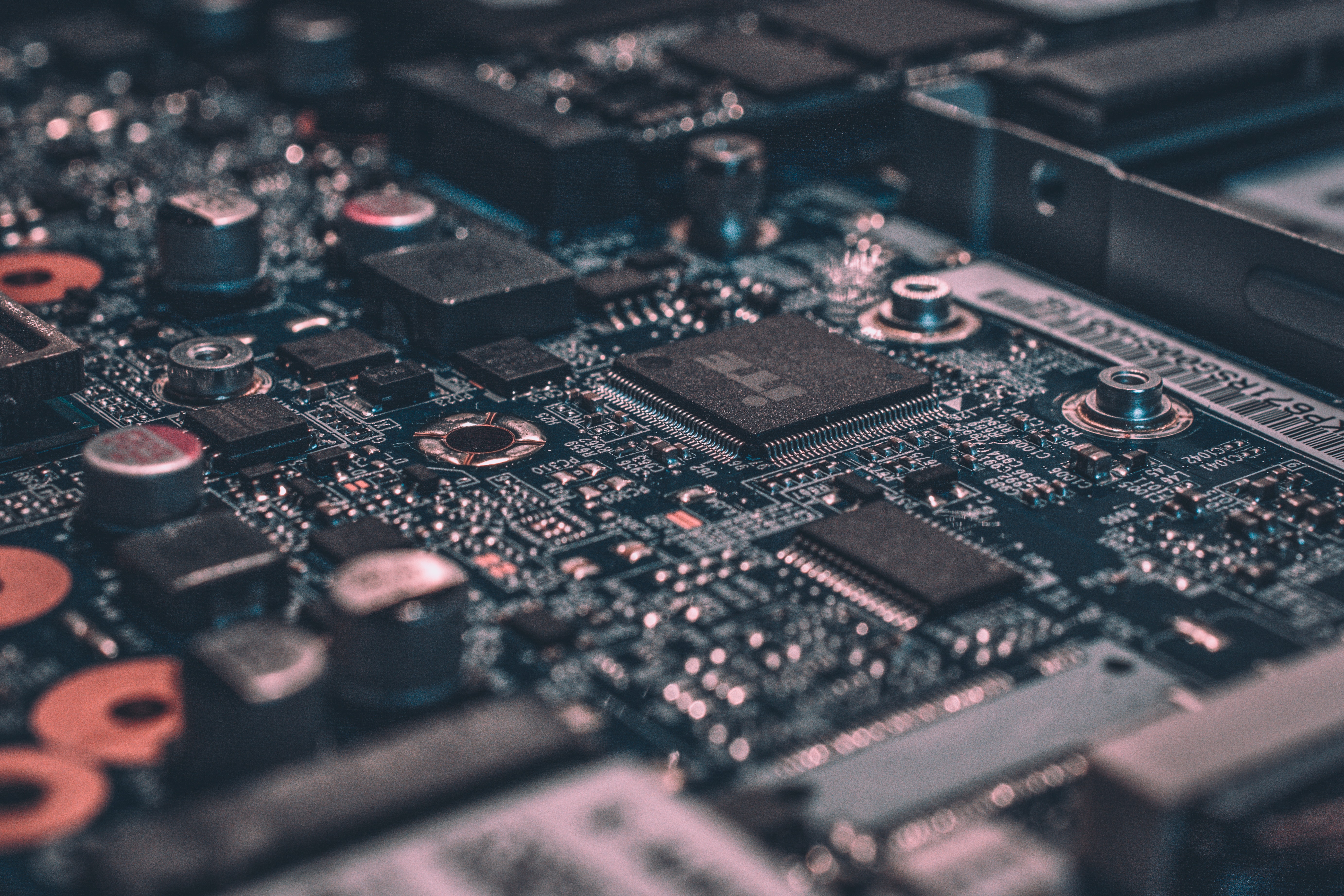
Building a powder coat oven may sound daunting, but with the right materials and knowledge it can be a straightforward and rewarding experience. Powder coating materials are essential in creating durable, beautiful finishes for all types of projects, from automotive to products around the home. A home-built powder coat oven can provide a cost-effective and efficient way to apply these materials and achieve the desired results.
The first step in constructing a powder coat oven is selecting the appropriate location for it. It should have plenty of air flow and space for safe operation, as well as adequate electrical outlets for power tools. Make sure you also have ventilation available, either through an exhaust fan or another external source such as a window or garage opening.
Once you have selected the appropriate location for your oven, you need to purchase all of the necessary materials required to make it functional. The most important requirement is insulation material such as ceramic fiber board or fiber blanket insulation that can maintain an even temperature throughout the enclosure. You should also consider purchasing high temperature thermocouples or thermometers to measure inside and outside temperatures within your powder coat oven. You also need mild steel or stainless steel sheets to create the frame of your oven which will contain everything else within it. Lastly you need one or more heating elements depending on your desired heat range in order to generate enough thermal energy to reach ideal temperatures necessary for powder coating applications
Finally, connect all components together with the appropriate wiring like 240V circuits dedicated for the heating element with its own breaker then connect ground wires from each component properly in order to strengthen stability of your oven enclosure in case of voltage fluctuations and thus preventing any damages due to improper connections.
If you follow these steps carefully you will have created a safe, reliable powder coating oven with plenty of heat capacity that can be used over years in whatever project comes along!
Here's an interesting read: Oven Safe Symbol
What materials are needed to construct a powder coat oven?
A powder coat oven is a popular way to protect and decorate metal surfaces from the everyday wear and tear of time. Constructing one requires several materials, each of which can have critical implications on the outcome of your finished product and its long-term durability. Knowing what is necessary and using quality materials are essential for successful construction.
The first material required for constructing a powder coat oven depends on what style you prefer. If you are using an all-metal build, steel or cast iron works best, both of which should be coated in zinc or aluminum to prevent rusting. For insulation, fiberglass mats and calcium silicate boards will help keep heat levels consistent while protecting other parts of your oven from damage due to increased temperatures. Next, two layers of aluminum foil will act as another layer of insulation before sheets of 20-gauge stainless steel line up against it for the interior walls. Finally, heavy duty hinges must be installed at each opening as well as a sealant for the door frame to avoid any heat escaping during use.
Other miscellaneous materials can be head such as protective gloves during construction, sealants in areas prone to exposure from high temperatures or humidity, and foam gaskets when needed for various components. Knowing how much material you need is another key consideration; to prevent any wasted purchases, measure twice and buy once! A little planning goes a long way in getting your oven customized perfectly for its desired purpose.
These materials create a powder coat oven with proper insulation that protects material components while ensuring heat consistency throughout the curing process. The utilization of these materials operate within building code regulations while creating an effective tool not only used efficiently but safely too. With the right pieces in place, you'll have the perfect powder coat oven without compromising on any details!
Recommended read: How Long for Oven to Cool Down?
How long does it take to build a powder coat oven?
Building a powder coat oven can be an exciting undertaking, but it is important for builders to know just how long it will take to construct. Generally, the process of creating a functioning oven for powder coating can take anywhere from four to eight weeks, depending on the size and design of the oven.
To begin, the builder should create a comprehensive plan that outlines the desired features and operational needs of the project. Once this is finalized, designs should be created for each individual element of the oven. Typically, this includes an insulated enclosure, burner assembly for heat source, automated thermostat for temperature control, and various exhaust fans to alleviate smoke and other emissions. After these are all constructed and approved by regulatory authorities (if necessary), assembly can begin.
The actual assembly of all components usually takes between two to three weeks. This includes laying out all pieces in their respective places inside the oven enclosure; fastening them securely with screws and steel bolts; connecting wires to ensure proper electrical grounding; attaching any necessary support beams or braces; and ensuring all components are sealed from outside contaminants. Construction may not seem like much at first glance, but testing each component as it is added is important for optimizing its performance over time–a process which takes time itself due to its labor-intensive nature.
Once all pieces are in their proper places and working correctly, it's time to break in your new equipment with some real-world use! Taking full advantage of your customized powder coat oven requires careful care and maintenance–but that's another blog post altogether!
What safety measures should be taken when constructing a powder coat oven?
Powder coating ovens are a key component in industrial manufacturing, allowing for surface coating of a wide range of objects. These ovens require safety measures for proper use, given the large amounts of heat within the area. It is highly important to consider the following precautions when constructing a powder coat oven:
First and foremost, fireproofing is crucial around any industrial machinery that uses consistent heat. Since powder coating ovens use heated air circulated through the entire working area, it is important to ensure that fireproofing materials are used along the walls and ceiling of the workspace. This includes insulation, fire retardant paints, and other specialized treatments. Fireproofing materials should also be used for any electrical components in proximity to the oven, such as wiring and igniters.
Continuing with safety measures – ventilation should be a primary focus when constructing a powder coat oven. The air inside must be constantly cycled out of the working environment through an effective ventilation system in order to both reduce hazardous fumes and keep temperatures regulated. A well-designed and maintained ventilation system can go far in reducing health risks associated with improper air circulation.
Finally, building the powder coat oven with quality components is another must-have safety measure. This includes using durable materials that have been specifically designed for high temperature settings as well as implementing regular maintenance on all equipment parts to ensure their proper functioning and stability during operation. Doing so decreases the likelihood of equipment failure or malfunctions which can result in unexpected risks from mishandled heat sources or electrics.
To sum it up – any person responsible for constructing a powder coat oven should prioritize fireproofing and ventilation aspects of construction alongside using quality components for sustained safety during operation.
Related reading: Wall Ovens
How does a powder coat oven work?
A powder coating oven is an essential tool in the powder coating process, and understanding how it works is key to a successful end product. With the right equipment, high-quality results can be obtained in a variety of applications.
Powder coated items are placed in an oven after they are painted with special powders. The oven applies heat which causes these powders to melt onto the surface of the item, forming a protective layer that gives it an attractive and durable finish. The temperature of the oven needs to be controlled very precisely in order for the powder coating to adhere correctly without discoloring or cracking. A digital controller is typically used to maintain the desired temperature for different products and processes.
Additionally, for cleanliness purposes and to ensure professional grade quality items, some powder coat ovens use air filtration systems that capture any over spray from other parts being applied in areas surrounding the oven. The air circulated by these systems also helps avoid clusters of particles settling on items as they are cured, creating an even finish on each piece.
When fully tuned and prepared for use, using a powder coat oven properly will provide consistent results with great finishes every time – ideal for industrial manufacturers who demand excellence and precision work.
What size oven is appropriate for powder coating?
Powder coating is a great way to give your car, patio furniture, or any other metal surface an attractive, durable finish. It’s a much simpler process than traditional paint and more cost effective as well. One of the key pieces of equipment you’ll need for successful powder coating is an oven. But what size is appropriate for the job?
The size of your oven will be determined by the size of your project and the amount of powder you’ll need to use. A larger oven should be used for wider, longer items such as metal patio furniture pieces or a car frame. Smaller ovens might suffice for smaller items such as decorative hardware or small parts baskets. Generally, an oven with at least six feet wide and three feet deep will be effective in providing enough space to accommodate most projects while still allowing air circulation. If you’re doing large projects that require large quantities of powder, look for an oven with a greater depth, such as four feet deep or more.
If you're just starting out with powder coating, you don’t have to invest in an industrial-level oven right away; it might not be necessary if working on smaller projects with limited amounts of powder. In those cases, only needing to coat a handful at the same time can often be handled adequately in a home-style oven. However, considering these types of standard electric ranges tend to lack specific features useful in powder coating—like extended lengths and widths—you should always do careful research before investing so that you're equipped with the best tools for achieving good results on your projects.
Suggestion: Cure Powder Coat
What advantages does a powder coat oven offer over other types of finishing methods?
Power coating ovens offer a range of advantages that render them more appealing than other types of finishing methods. Firstly, powder coating is an environmentally friendly option as it does not release any chemical by-products into the atmosphere, unlike liquid painting. Secondly, the process is incredibly efficient as it does not require primer or additional coats like liquid paint might. As such, large batches or jobs may be finished far faster with power coating than any other type of finishing.
Moreover, powder coated finished products have a longer life span than their counterparts finished via other methods. This is due to their chemical resistance and general resilience to common abrasions and environmental issues such as UV light. Furthermore, powder coated finishes tend to be far more aesthetically pleasing and uniform than a traditional unfinished surface. The smooth glossy finish adds a level of sophistication to any product making them both visually pleasing and long lasting.
For these reasons power coating in an oven is often the preferred method of finishing for metal parts and components across many industries including aerospace and automotive applications. Business owners looking for an efficient, economical and environmentally friendly way to finish metal components should consider the advantages that a powder coat oven offers over other methods available today.
Take a look at this: Why Does My Oven Keep Smoking?
Sources
- https://thermcraftinc.com/5-benefits-of-powder-coating-ovens/
- https://bmmagazine.co.uk/business/what-is-a-powder-coating-oven-used-for/
- https://www.ovenhomes.com/powder-coating-oven-how-much-cost/
- https://www.powdercoatguide.com/2014/09/how-to-build-powder-coating-oven.html
- https://www.powdercoatingonline.com/powder-coating-ovens-and-oven-maintenance/
- https://houseax.com/how-to-build-your-own-powder-coating-oven/
- https://www.rileysurfaceworld.co.uk/knowledge/why-do-you-need-an-oven-for-powder-coating/20.htm
- https://lightarmor.us/blogs/news/how-does-powder-coating-oven-work
- https://www.ovenhomes.com/diy-powder-coating-oven-plans-and-tutorials/
- https://www.mintdesignblog.com/diy-powder-coating-oven-plans/
- http://powdercoatingonline.com/wp-content/uploads/2015/07/ovendesign.pdf
Featured Images: pexels.com