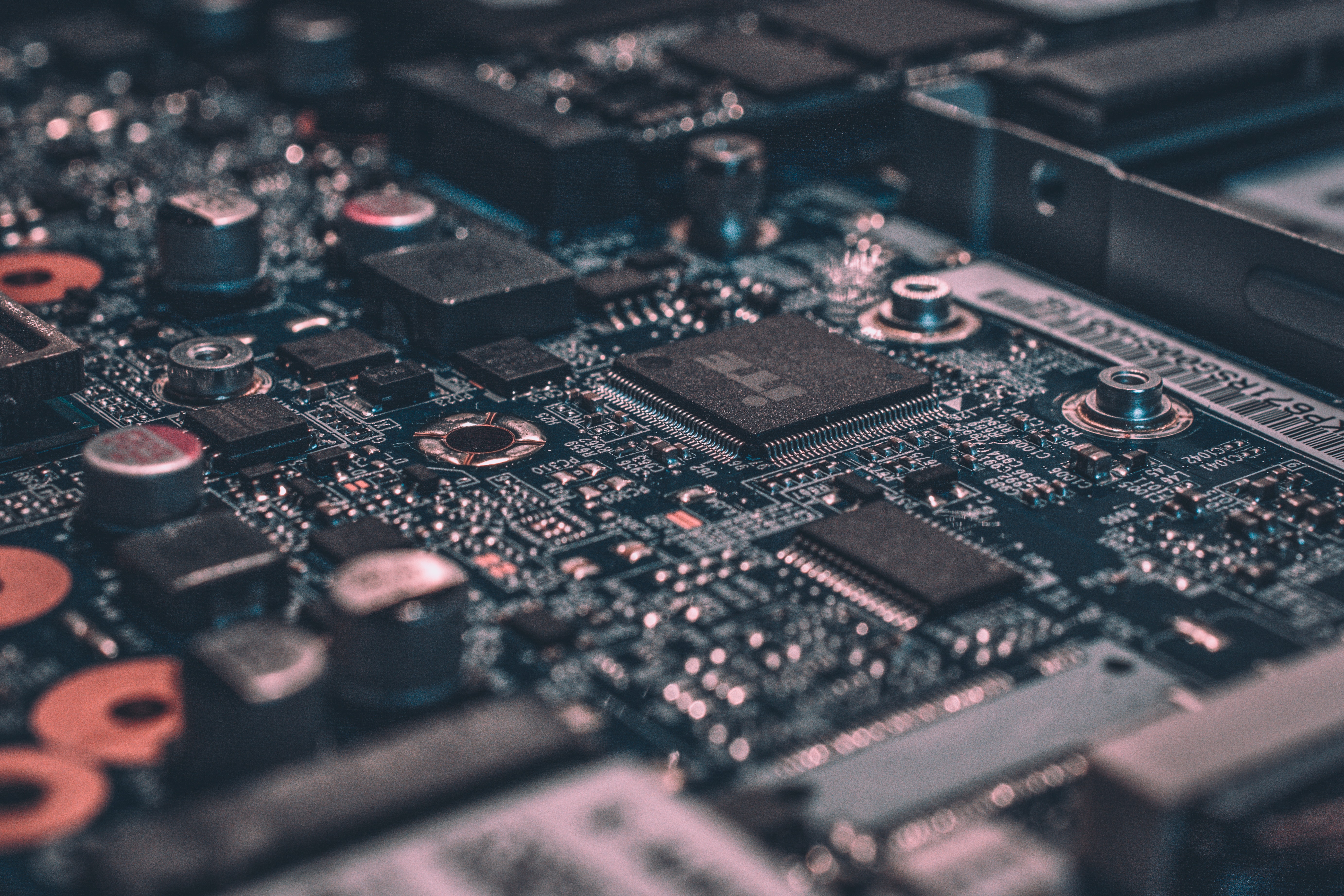
3D printing can be a great way to produce both prototypes and top-notch finished products. However, the process is not without its challenges. One issue that can occur is warping of the 3D print. Warping occurs when the edges curl or pull away from the flat surface of the 3D printed object due to differences in cooling rates of different materials used in the 3D printing. Under certain conditions such as faulty filament or improper settings in the printer, this can result in a warped finished product.
Fortunately, there are some measures you can take to prevent warping after your 3D print is complete. The first step is ensuring that your filament is free of any defects or inconsistencies. Make sure that it fits in properly into your nozzle and that it extrudes evenly to create uniform layers when printing. If possible, experiment with different types of filaments and temperatures to ensure optimal results for your product.
One key factor that affects warping when printing is temperature—both inside and outside of your printer while creating your product. Make sure that your printer’s internal temperature stays consistent throughout the process, as this ensures that all parts are cooled at the same rate, reducing warping effects. If you do not have a temperature control system for printing then it may be beneficial to set up a controlled environment around your product where constant temperature conditions can be maintained during the entire printing process from start to finish (such as an air conditioner). This will not only help you prevent warping but also improve print quality overall!
In addition to controlling filament use and internal temperatures, using a heated bed for 3D prints can also help significantly reduce distortion and improve adhesion between layers which ultimately results in stronger bonds as well as improved print integrity overall. This is especially important when working with ABS filaments as they are particularly prone to warping so having a heated bed with adjustable temperatures can make a big difference! Finally, be sure to use quality supports to hold up any overhanging areas before they cool completely otherwise they may end up sinking and resulting in an uneven surface on top of the part creating uneventh cooling all around which could lead potentially lead again to distortion.
By following these simple tips you will be able not only reduce succesfully warpings but also help you maximize print quality together with reliability!
For your interest: How to Prevent Website Crash from Traffic
What materials can be used to reduce warping in 3D printing?
The use of 3D printing is becoming increasingly popular, particularly in the manufacturing and engineering industries. But while 3D printing can provide unparalleled control of intricate designs, it also comes with some problems. One of the most common issues when it comes to 3D printing is warping. This occurs when one part of the material being printed cools faster than other parts of the material, resulting in a warped shape on your finished product. Warping can be especially problematic for larger prints that may take hours or even days to finish.
Thankfully, there are a few materials you can use to reduce warping and drastically improve the print quality of your 3D printed objects. ABS (Acrylonitrile Butadiene Styrene) is one of the most popular materials for reducing warping, as it comprises a strong rigidity along with thermal insulation properties that reduce temperature differences across your object during printing. Additionally, ABS heats up more slowly than PLA (Polylactic Acid), allowing you to print without risking a sudden drop in temperature while the printer is still running.
Another material you can use to help mitigate warping is nylon-based filament – nylon has excellent layer adhesion which makes it great for large builds since it reduces warpage significantly. It also offers superior strength due to its flexibility and toughness, making it perfect for highly intricate prints that require great accuracy and detail. Similarly, PETG (polyethylene terephthalate glycol-modified) has also shown promising results in reducing warpage while producing highly detailed prints - this type of filament has temperature resistance properties allowing higher temperatures during printing without risk of melting or cracking.
Ultimately by using materials specifically designed for 3D printing such as ABS, nylon-based filaments or PETG you can significantly reduce the chances of encountering warped parts in your design; these materials offer insulation and cooling benefits that prevent significant temperature discrepancies thus reducing any potential distortions over time during printing stages.
A fresh viewpoint: Dye 3d Printed Nylon
How can overheating be avoided in 3D printing to reduce warping?
Overheating can cause warping in 3D printing, which is not only problematic but also leads to waste in materials, time, and money. To prevent warping due to oveheating in 3D printing, there are several measures a user can take.
Firstly, it is important to adjust the printer temperature to match the type of filament being used. Overheating can be caused by a substrate heated at too high of a temperature while the plastic material used has a lower melting point. Secondly, users should ensure all heated surfaces on the printer bedinsulated and configured correctly; turning off insulation when not necessary will help minimize overall heat generated from the machine.
Thirdly, user should take into consideration the ambient environment during 3D printing process--the room ambient temperature might affect how quickly an object is heated up and cooled down; therefore be sure to keep an optimal room temperature for efficient outcomes. Finally, using cooling fans for objects will also help by cooling down extruded plastic quickly so that it maintains its shape without warping. Taken together, these strategies can not only help users produce good quality prints with minimal irregularities from warping but also help save time and cost in regards to material waste.
Check this out: 3d Printer Print
What techniques can be used to decrease warping in 3D printing?
3D printing has become an increasingly popular and cost effective solution for creating tangible models of 3D designs, but a common problem with this technology is warping. Warping occurs when the plastic filament cools down at different rates causing the plastic to create too much tension in specific points and change the shape of a 3D printed object. Thankfully, there are some clever techniques that can be used to reduce warping and keep your 3D prints looking flawless.
The first technique to reduce warping is proper film cooling. This means that you need to give the printed object enough time to cool down after being printed. The cooling period should last for long enough that the temperature differential decreases, allowing for reduced tension in higher powered areas of the plastic and, thus, reduced warping. Keeping a consistent environment temperature is also an important factor when it comes to reducing warping. The more constant the temperature, whether hot or cold, the less internal shifts of cooling will occur within a print job causing further reduction in tension-caused warping issues.
Another technique to reduce warping is printing with materials better suited for FDM (Fused Deposition Modeling). ABS (Acrylonitrile Butadiene Styrene) filaments are particularly prone to warping due to the large differences in cooling happening during and after production. Switching over to materials such as PLA (Polylactic Acid) or PETG (Polyethylene terephthalate Glycol-modified) can decrease tension due their higher glass transition temperatures which will cause slower cooling.
Each technique combined should result in decreased warpage making your 3D prints look flawless and professional every time you print them out.
Related reading: Plastic Cups Diy
How can support structures be used to increase parts strength and reduce warping?
Support structures are commonly used in a variety of industries. In engineering, these structures are utilized to increase a part’s strength, rigidness and performance by preventing warping or deformation of the part due to specific loads or forces.
Using various types of support structures can help increase the part’s overall strength by making it more resilient and resistant to impacts, vibrations, and other external forces. Depending on the nature/complexity of a product’s design, a combination of different support materials may be required to create an effective support structure.
For instance, when creating complex curved parts, designers may rely on using multiple ribs inside the wall of the component to give it additional rigidity. This maximizes the strength at each point with two radial ribs completely surrounding each corner node on the shape itself, which significantly reduces warping due to transverse forces on that section of the component. In addition, high-strength composite materials are often combined with foam sheets between layers in order to give extra rigidity without increasing weight significantly or adding cost prohibitively.
Support structures are an essential engineering design element that enhances components’ strength and reduces warping issues caused by external forces. Designers must carefully select materials that ensure its optimal performance and meet design requirements in cost-effective shapes and sizes for maximum efficiency and reliability of their product. With intelligent design strategies such as this one in place, parts can be made much stronger with minimal additional weight or cost.
Discover more: Lenticular Printing Cost
What post-processing techniques can be used to minimise warping in 3D printed parts?
3D printing technology has come a long way in recent years, making it more affordable than ever to create intricate shapes with the right 3D printer. But one of the challenges that can occur when attempting to 3D print parts is warping, where the edges of a printed piece curl or distort due to temperature differences in different parts of the item. Fortunately, there are a few post-processing techniques you can use to minimise warping after 3D printing and make sure your parts look their best.
One technique that can help reduce warping is cooling with a fan. To use this method, enclose your build plate with something rigid like a cardboard box or something with four sides and install a small fan into it. Start by positioning one of the fans near the top front part of the box and then slowly lower it until you feel some air pressure on top of your build plate. This will cool down the whole item which can help reduce warping and make sure parts will stay straight for longer time periods.
Another technique that can be used is surface adhesion control where thermal glue or spray adhesive is applied onto your build plate before starting the print job. This helps build adhesiveness between the printed item and its base so that as it cools down all at once, distortion rarely occurs and warping is reduced significantly upon completion.
Finally, a post-processing technique known as cold pulling might also be worth considering if you’re serious about minimising warping in 3D printed objects. Cold pulling involves heating up both sides of your item up to around 95 degrees Celsius and then using two pairs of needle nose pliers to pull inwards all around each side simultaneously, thus ensuring that everything stays in place once cooled down again. After cold pulling your items should remain perfectly straight without any warping or distortion whatsoever.
These are just some post-processing techniques you can use an attempt to minimise warping in 3D printed parts, but ultimately there’s no guarantee they will work perfectly every time since there are many variables that could still cause distortion even after cooling your parts or controlling surface adhesion levels properly. If you truly want consistent results every time, professional equipment like heated beds might be worth looking into as well as specialised software solutions like MeshMixer which provide numerous other tools for preventing warps during printing jobs too.
Additional reading: Curved Surface
How can print settings be configured to reduce warping in 3D printing?
Warping can be an annoying side effect of 3D printing and a genuine impediment to the success of a designed piece. It is often caused by improper settings within the specifications, as well as environmental factors such as extruder temperature, filament characteristics or surrounding air temperature. Fortunately, one can take steps to reduce warping by fine-tuning a range of print settings.
The first thing to consider is thermal management. During the printing process, thermoplastics – such as ABS and PLA – will increase in temperature and cool down when extruded from the nozzle. To minimize warping, ensure that temperatures remain consistent at both the nozzle and heated bed (if available). By using an insulation board and cooling system on top of the model base, it becomes easier to maintain temperatures between layers.
Another tip is gearing up on adhesion materials and methods. All too often it is assumed that a heated platform provides strong adhesion between layers; but without additional adhesion materials or post-processing techniques, warping may still occur during or after printing. Applying blue painter’s tape or gluing ABS juice onto the build surface offers improved adhesion between layers that helps fight warping mid-print. Meanwhile, some users prefer post-processing options like sanding or polishing to improve layer adhesion after printing.
Finally, modifying your slicing settings can also reduce warping during 3D printing processes. Many slicers feature options that affect how quickly each layer is built; either increasing or decreasing these values may help depending on your environment during printing. Furthermore, attempting to keep thin walls overhangs high so they can form their own support layer should further reduce warping in certain designs and prints!
By understanding which print settings are most likely to lead to more successful prints with minimal warping – including thermal management strategies for heating beds and nozzles; increased adhesion; and modified slicing settings – 3D printing professionals have better chances of achieving their desired results with fewer flaws.
Related reading: 3d Printer Nozzle
Sources
- https://www.3dsourced.com/rigid-ink/3d-prints-warping-curling-how-to-prevent/
- https://3dprinterly.com/are-your-prints-warping-or-curling-learn-how-to-fix-it/
- https://waykenrm.com/blogs/3d-printing-warping/
- https://twotrees3d.com/3d-printing-warping/
- https://www.matterhackers.com/news/-how-to-stop-filament-warping-in-3d-printed-parts
Featured Images: pexels.com